Data in logistics operations
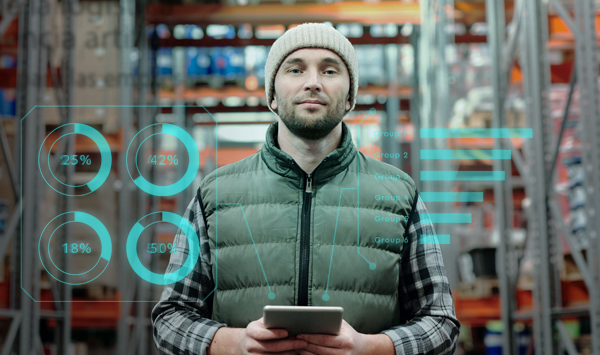
Logistics operations are facing a major challenge: channeling and making sense of the data they generate on a daily basis, which is no small amount.
Market demands, the implementation of new technologies and globalization are bringing about a change in the way logistics processes are managed and resources are allocated.
However, it is still surprising to see the number of companies with logistics departments that turn their backs on digital transformation, thereby losing quality in their delivery service, slowing response times and, in short, not achieving the level of customer satisfaction or the sales figures they would like. For all these reasons, it is essential to have a great ally that allows us not only to optimize processes, but also to be able to react to any unforeseen event, anticipate trends and provide excellent customer service. Who is it? DATA.
It is overwhelming, impatient, and unemotional. He surrounds us. He strolls through our company like a pensioner in the park, remembering the past, and with a look full of experience. We contemplate him with the appearance of interest, but with the feeling that he will be of little help to us. However, he hides so much knowledge that we should find a way to pay more attention to him.
Data analytics has a strong power when it comes to managing a company and, specifically, logistics departments. They are the key piece of the puzzle. The data and, of course, the correct interpretation of them, are what will allow us, on the one hand, to recognize and analyze the state in which our company is (where we are doing well, where we are doing badly, what processes we can improve); on the other hand, to make the right decisions and, moreover, in a very agile way and away from any assumption.
The supply chain, more interconnected than ever before
Logistics departments must coordinate an enormous amount of materials and resources: arrival and departure schedules of the fleet of trucks and/or ships, control of containers (by type of goods, tonnage, destination and origin, etc.), management of the rotation of schedules, etc.
In this way, and in order to give a logical sense to the information, it is essential to capture, monitor and visualize the information in business dashboards. A technological solution that allows us, not only to convert information into knowledge, but also to make coherent decisions very quickly.
But where do we start to set up our dashboard?
Definition of an objective and choice of KPIs
What do we want to achieve with our dashboard? Maybe we want to speed up the delivery times of the goods, improve customer satisfaction, reduce the response time to any incident?
Whatever our purpose is, the important thing is to know where we want to get to, because it will be decisive to choose the indicators or KPIs that will be displayed on the dashboard. Thus, in a very visual and intuitive way, we will know the points where we can improve, what we are doing well and, in short, where we should focus our efforts.
Although it is true that each department will have specific needs depending on the logistics operations they perform, there are certain indicators that must be consulted. Here are some examples:
- Geolocalization of orders.
- Order routing (origin, destination, distance, date and estimated time of arrival).
- Detail of carriers: name, assigned orders…
- Container type.
- Status of main sea and dry ports.
- Type or order: import/export.
- Available trucks.
Giving value to the team
Behind every decision there is always a work team. Therefore, when planning a dashboard we must think about the people who are going to consume the information and capture the data that will really help to make the right decisions. In addition, the team, at a glance, must be able to draw conclusions quickly and detect any anomaly (for example, where the goods are, if there are delays in delivery due to an accident or road closures, if there is more or less traffic, if there is inclement weather, etc.).
Having all this information in real time and at a glance gives us an incredible capacity to make decisions quickly, to detect any alert (with a color indicator, for example, that changes according to the seriousness of the situation) and to act instantly. Not only do we save time, but also money (and a lot of it!).
In short, the development of a technological project that provides real-time information on logistics operations is crucial to improve the performance of any supply chain. The correct selection of metrics and their monitoring and visualization in real-time brings with it an undeniable improvement in competitiveness and helps us to define specific improvement actions.
And you, are you turning your back on digital transformation?